Personal Protective Equipment (PPE) is an essential safety measure in various industries that involves exposure to hazards such as physical, chemical, biological, or environmental. PPE is designed to protect the worker from potential hazards that can cause injury or illness. PPE includes clothing, helmets, goggles, gloves, and other equipment that provides a physical barrier between the worker and the hazardous elements. In this article, we will discuss the different types of PPE, technical aspects, and standards required
Regarding the statistics on how many accidents were avoided by using PPE, again, it is challenging to provide an exact figure. However, studies have shown that PPE can significantly reduce the risk of injuries and illnesses in the workplace. For example, a study by the Occupational Safety and Health Administration (OSHA) found that PPE was estimated to prevent or reduce the severity of injuries and illnesses in approximately 21% of cases.
Another study by the National Safety Council found that workers who wore PPE reduced their risk of eye injuries by 90%, head injuries by 85%, and foot injuries by 60%. Therefore, it is clear that using PPE can make a significant difference in reducing the number of accidents and injuries in the workplace.
According to a report by Grand View Research, Inc., the global PPE market size was valued at USD 43.9 billion in 2020 and is expected to reach USD 95.5 billion by 2028. So PPE is a important aspect of Safety
Table of Contents
Technical Aspects of Personal Protective Equipment
When it comes to selecting PPE, it is essential to consider its technical aspects. The PPE must meet the standards and regulations set by the industry and the government to ensure maximum protection to the worker. The selection of PPE depends on the industry and the specific hazards a worker is exposed to. However, there are critical technical aspects that must be considered when selecting PPE, regardless of the industry. These aspects include resistance to penetration, durability, fit and comfort, visibility, and chemical resistance
Technical aspects of PPE include:
Resistance to penetration: PPE must provide a physical barrier to prevent hazardous elements from penetrating the material. The material used in making the PPE should be able to withstand the physical stress and prevent any harmful substances from entering the worker’s body.
Durability: PPE must be durable enough to withstand regular use without compromising its protective capabilities.
Fit and Comfort: PPE must fit properly to provide maximum protection and be comfortable to wear to encourage workers to use it consistently. improper-fitting PPE can compromise its protective capabilities and discourage workers from wearing it.
Visibility: PPE must be visible to ensure that workers can easily identify other workers wearing PPE. This aspect is crucial in ensuring all workers adhere to PPE guidelines.
Chemical Resistance: PPE must resist the corrosive effects of chemicals to protect the worker. This is especially critical in industries where workers are exposed to hazardous chemicals.
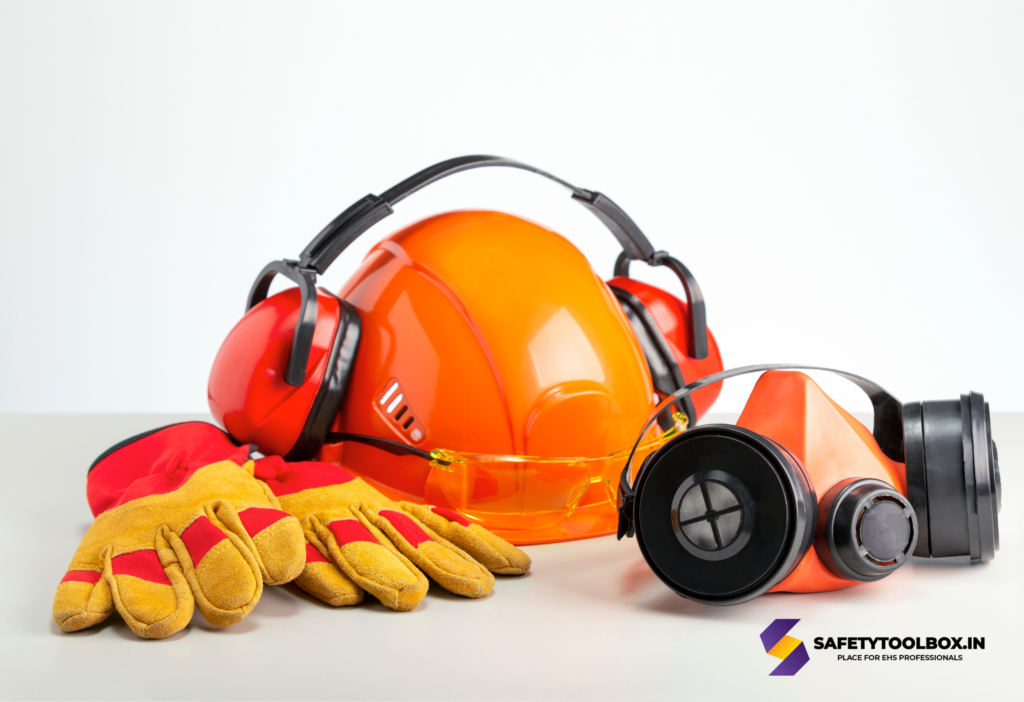
Standards Required for Personal Protective Equipment
To ensure the effectiveness of PPE, it is essential to follow the standards and regulations set by the industry and government. Some common standards required for PPE include:
American National Standards Institute (ANSI): ANSI sets standards for personal protective equipment in various industries, including construction, manufacturing, and healthcare.
National Institute for Occupational Safety and Health (NIOSH): NIOSH provides guidelines for the use and selection of respiratory protection equipment.
Occupational Safety and Health Administration (OSHA): OSHA sets standards for PPE in the workplace and provides guidelines for selecting and using PPE.
European Committee for Standardization (CEN): CEN sets standards for PPE in the European Union.
Types of Personal Protective Equipment
There are different types of PPE available to workers depending on the industry and the type of hazards they are exposed to. Some common types of PPE include:
Head Protection
Hard hats or helmets protect the head from impact, penetration, and electric shock hazards. They should be worn in any environment where there is a potential for head injury. Standard reference number: ANSI Z89.1-2014
Key consideration for Hard hats or helmets
Hard hats are required to feature a rigid exterior and a lining that absorbs shock, which should include a headband and straps that keep the exterior suspended 2.54 cm to 3.18 cm away from the head. This specific design offers ventilation during normal use and cushioning in the event of an impact.
Chose hardhat or safety helmet according to the work location, it divided in to three classes.
Class | Voltage Protection Up to | Other requirements |
Class- A | 2200V | Impact + penetration |
Class- B | 20,000V | Impact + penetration |
Class- C | No protection | Impact + penetration + light weight |
Eye and Face Protection
Safety glasses, goggles, welding shield and face shields protect the eyes and face from flying debris, chemical splashes, radiation, and other hazards. They should be worn in any environment where there is a potential for eye or face injury. Standard reference number: ANSI Z87.1-2020
Key consideration for selecting Eye and face protection
- Specific hazards protection capability
- Proper fit and comfortable to wear
- Unrestricted vision and movement while wearing
- Durable and cleanable for long-term use
- Allows unrestricted functioning of any other required PPE
Respiratory Protection
Respirators, masks (N95, half face mask, full face mask, dust mask), and air-purifying respirators (PAPRs) protect workers from inhaling hazardous chemicals, dust, and other harmful substances. They should be worn when exposure cannot be eliminated or reduced to acceptable levels through other controls. Standard reference number: NIOSH 42 CFR Part 84
Key Consideration for respiratory protection:
while selecting a respiratory include the level of protection required, the nature of the hazardous environment, the duration of use, the comfort and fit, and the user’s medical history

Hearing Protection
Earplugs, earmuffs, and other devices protect workers from loud noises and other sources of noise pollution. They should be worn when working in environments with noise levels above 85 decibels (dB) or in any environment where there is a potential for hearing loss. Standard reference number: ANSI S12.6-2016
The key considerations when selecting the right type of hearing protection for your needs include
Noise reduction rating (NRR): The NRR is a measure of how much sound reduction a hearing protection device provides. A higher NRR means that the device is more effective at blocking out noise. When selecting hearing protection, it is important to choose a device with an NRR that is appropriate for the level of noise you will be exposed to.
Comfort: Comfort is important because if the hearing protection is uncomfortable, it may not be worn consistently or for as long as needed. Earmuffs tend to be more comfortable for extended wear, as they do not need to be inserted into the ear canal.
Fit: It is important that the hearing protection fits properly to provide maximum effectiveness. Earplugs should be inserted snugly into the ear canal, while earmuffs should provide a good seal around the ear.
Convenience: Convenience can be a factor in selecting hearing protection, especially if it needs to be worn for extended periods. Earplugs can be more convenient to carry and store, while earmuffs can be more convenient to put on and take off quickly.
Communication: If you need to communicate while wearing hearing protection, it is important to choose a device that allows for this. Earmuffs can be designed with built-in communication systems or allow for communication through a microphone and speakers.
Compatibility: If you wear other personal protective equipment (PPE), such as a hard hat or safety glasses, it is important to select hearing protection that is compatible with your other PPE. Some earmuffs are designed to be worn with hard hats, for example.
Ultimately, the selection of hearing protection will depend on the specific needs and preferences of the user, as well as the noise exposure levels they will be experiencing.
Hand and Arm Protection
Gloves, sleeves, and other protective gear protect workers from cuts, burns, and other injuries. They should be worn when working with hazardous materials, sharp objects, or when handling equipment with potential pinch points. Standard reference number: ANSI/ISEA 105-2016
Key consideration to keep in mind to selecting gloves and sleeve
Material: Safety gloves and sleeves can be made from a variety of materials, including leather, rubber, latex, neoprene, nitrile, and more. The choice of material will depend on the specific hazards present, as well as the dexterity and grip needed for the task.
Cut resistance: If there is a risk of cuts or punctures, it is important to choose gloves and sleeves that are cut-resistant. This can be measured using various standards, such as the ANSI/ISEA 105 or EN 388. The level of cut resistance needed will depend on the level of risk present.
Chemical resistance: If there is a risk of exposure to chemicals, it is important to choose gloves and sleeves that are resistant to the specific chemicals present. The level of chemical resistance needed will depend on the type and concentration of the chemicals.
Heat resistance: If there is a risk of exposure to heat, it is important to choose gloves and sleeves that are heat-resistant. This can be measured using various standards, such as the EN 407. The level of heat resistance needed will depend on the temperature and duration of exposure.
Comfort and fit: It is important that gloves and sleeves fit properly and are comfortable to wear, as this can impact their effectiveness. Gloves and sleeves that are too tight or too loose can cause discomfort and impact dexterity.
Durability: The durability of gloves and sleeves will impact their lifespan and effectiveness.
Foot and Leg Protection
Steel-toed shoes, boots, and other protective gear protect workers from falling objects, sharp objects, and other hazards. They should be worn in any environment where there is a potential for foot or leg injury. Standard reference number: ASTM F2413-18
Key consideration for selection of foot and leg protection
Toe protection: Safety shoes should have toe protection, which can be made of steel, aluminum, or composite materials. The level of toe protection needed will depend on the hazards present, such as heavy objects that could fall on the foot.
Slip resistance: Safety shoes should have slip-resistant soles to reduce the risk of slips and falls. The level of slip resistance needed will depend on the working environment, such as wet or oily surfaces.
Electrical hazard protection: If there is a risk of electrical hazards, such as electrical shock or electrostatic discharge, safety shoes should have electrical hazard protection. This can be indicated by a specific ASTM standard.
Comfort and fit: Safety shoes should fit properly and be comfortable to wear for extended periods of time. Poorly fitting shoes can cause discomfort and reduce productivity.
Durability: Safety shoes should be durable and able to withstand the wear and tear of daily use. Shoes that wear out quickly may need to be replaced more frequently, which can impact cost.
Body Protection
Coveralls, vests, and other protective clothing protect workers from exposure to hazardous materials or extreme temperatures. They should be worn when working with hazardous chemicals, extreme temperatures, or when exposed to radiation. Standard reference number: ANSI/ISEA 101-2014
For key consideration of hi-vis visit here
Fall Protection PPE
Falls are a significant hazard in many industries, including construction, manufacturing, and transportation. According to the Occupational Safety and Health Administration (OSHA), falls are the leading cause of fatalities in the construction industry. To prevent falls, workers must wear appropriate fall protection PPE, including:
Fall Arrest Systems, safety nets, safety belt, retractable fall arrestor, lifeline these all systems are designed to stop a worker who has fallen and prevent them from hitting the ground
Here are some key considerations:
Length: The length of the lanyard should be selected based on the distance between the worker and the anchor point. It is important to choose a lanyard that is long enough to allow for movement, but not so long that it allows the worker to fall a significant distance.
Material: Lanyards can be made from various materials, such as nylon or polyester. The choice of material will depend on the specific working environment, as well as the level of durability and comfort needed.
Shock absorption: Some lanyards are designed with shock-absorbing properties, which can reduce the impact of a fall. The level of shock absorption needed will depend on the height of the fall and the weight of the worker.
Connector type: The connector type should be selected based on the anchor point and the worker’s personal preference. Common connector types include snap hooks, rebar hooks, and carabiners.
Weight capacity: The weight capacity of the lanyard should be selected based on the weight of the worker and any equipment being used. It is important to choose a lanyard with a weight capacity that is greater than the total weight being supported.
Compatibility: The lanyard should be compatible with the other components of the fall protection system, such as the harness and anchor point. It is important to choose components that are designed to work together to provide maximum safety.
Inspection and maintenance: It is important to regularly inspect and maintain the lanyard to ensure it remains in good working condition. The manufacturer’s instructions should be followed for proper inspection and maintenance procedures.
Why is PPE Necessary?
PPE is necessary to protect workers from workplace hazards that can cause injury or illness. However, it is important to note that PPE is the last line of defense and should be used only when all other methods of hazard control have been exhausted. This approach is known as the Hierarchy of Controls, which prioritizes the most effective hazard control methods in the following order:
Elimination: Remove the hazard entirely.
Substitution: Substitute hazardous material or process with less hazardous material or process
Engineering Controls: Isolate the worker from the hazard. For example, installing ventilation systems to reduce exposure to harmful fumes.
Administrative Controls: Change the way work is done. For example, limiting the time of exposure to a hazard.
Personal Protective Equipment: Provide PPE to the worker as a last line of defense.
How to choose Right PPE?
When selecting PPE, it is essential to choose the right type of PPE for the job. It is also important to ensure that the PPE meets the appropriate safety standards. Here are some guidelines for selecting the right PPE:
Conduct a Workplace Hazard Assessment: The first step is to assess the workplace for potential hazards that can cause harm to workers. This can be done by conducting a workplace hazard assessment that identifies the potential hazards, evaluates the risks associated with each hazard, and determines the appropriate control measures to be put in place.
Identify PPE Needs: Based on the results of the workplace hazard assessment, identify the PPE needed to protect workers from the identified hazards. PPE should be selected based on the level of risk associated with the hazard and the effectiveness of the PPE in mitigating the hazard.
Determine the Type of PPE: Determine the type of PPE required for each hazard. PPE types can include eye and face protection, head protection, foot protection, hand protection, and respiratory protection, among others.
Ensure Proper Fit: Ensure that the selected PPE fits properly and is comfortable for the worker to wear. Improperly fitting PPE can reduce its effectiveness and increase the risk of injury.
Train Workers: Train workers on the proper use, care, and maintenance of PPE. Workers should understand when and how to use PPE, how to properly inspect and maintain it, and how to store it when not in use.
Regularly Review and Update PPE: Regularly review and update PPE requirements as needed. As new hazards are identified, or as new PPE technologies become available, it may be necessary to modify or upgrade the PPE used in the workplace.
By following these step-by-step methods, employers can identify the PPE requirements for their workplace, help prevent workplace injuries, and promote a safe working environment.
Inspection and maintenance of PPE
PPE must be inspected regularly to ensure it is in good condition. Damaged PPE must be replaced immediately.
Inspecting personal protective equipment (PPE) is a crucial part of ensuring its effectiveness in protecting workers from potential hazards. Here are the steps for inspecting PPE:
Conduct a visual inspection: Start by conducting a thorough visual inspection of the PPE. Look for any signs of damage, wear and tear, or contamination. Check for cracks, dents, holes, tears, or any other visible defects.
Check for proper fit: Verify that the PPE fits properly and is adjusted correctly for the individual worker. Make sure that the equipment is snug but not too tight, and that there are no gaps between the PPE and the skin.
Review manufacturer’s instructions: Review the manufacturer’s instructions and guidelines for inspection and maintenance of the PPE. Follow the recommended schedule for inspections and replace the PPE as required by the manufacturer.
Conduct a functional test: Test the PPE to ensure that it is still functional. For example, test the air-purifying respirator by checking the airflow, or the earplugs by squeezing them and checking for resilience.
Replace damaged or worn out PPE: Any PPE that has visible damage, excessive wear and tear, or has exceeded its recommended lifespan should be replaced immediately. Do not try to repair or modify the PPE on your own.
Document your inspection: Keep a record of the inspection and the replacement of any PPE. This documentation can be used to track the maintenance schedule and to demonstrate compliance with safety regulations.
Remember that regular inspection of PPE is necessary to ensure that it provides the necessary protection to workers. Follow the manufacturer’s instructions for the inspection and maintenance of PPE and replace any damaged or worn out equipment immediately.
Guidance document of OSHA for PPE
“Occupational Safety and Health Administration (OSHA) Standards for Personal Protective Equipment” – This is a comprehensive guide that provides information on the requirements for PPE in various industries as outlined by OSHA.
Download by clicking below button
Top PPE manufacturers in the world
3M : 3M is a US-based multinational company that produces a wide range of personal protective equipment, including respiratory protection, hearing protection, eye and face protection, and more.
Honeywell : Honeywell is a US-based company that produces personal protective equipment
Ansell : Ansell is an Australian-based company that produces a wide range of personal protective equipment, including gloves, clothing, and other protective gear
DuPont : DuPont is a US-based company that produces a wide range of personal protective equipment, including protective clothing, gloves, and footwear
MSA Safety : MSA Safety is a US-based company that produces a wide range of personal protective equipment, including respiratory protection, fall protection, and industrial head protection.
Kimberly-Clark : Kimberly-Clark is a US-based company that produces a wide range of personal protective equipment, including gloves, masks, and protective clothing
Lakeland Industries : Lakeland Industries is a US-based company that produces a wide range of protective clothing and accessories
Alpha Pro Tech : Alpha Pro Tech is a US-based company that produces a wide range of personal protective equipment, including masks, gowns, and face shields
uvex safety : uvex safety group is a German-based company that produces a wide range of personal protective equipment, including protective eyewear, respiratory protection, and hearing protection
Dräger : Dräger is a German-based company that produces a wide range of personal protective equipment, including respiratory protection, gas detection, and medical equipment
Moldex-Metric : Moldex-Metric is a manufacturer of hearing and respiratory protection, as well as other PPE products.
For regular updates on safety topics or videos follow us on linkedin
for more toolbox talk click here…
very informative
Greetings!
Thank you for all your efforts that you have put into this. very interesting information.
Thanks so much
Thanks, it was very useful
The information provided is very detailed and benefiting